Case Study Compiled by
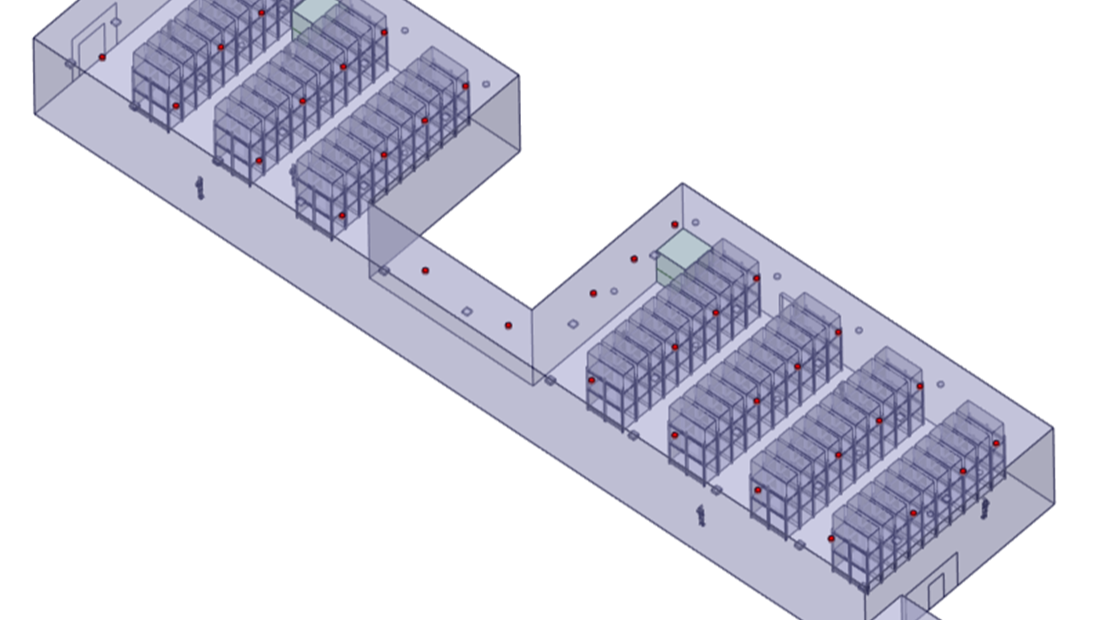
3D CAD MODEL OF WAREHOUSE
Brief of case study
This case study explores how CFD analysis was used to optimize HVAC performance in a pharmaceutical warehouse, ensuring cGMP compliance and energy efficiency. By analyzing airflow distribution, temperature control, and humidity regulation, the study highlights key improvements such as uniform cooling in the acceptable range of 18 - 24°C, elimination of stagnant zones, and relative humidity stabilization below 60%. The optimized design not only enhanced product safety by eliminating hot spots but also reduced HVAC energy consumption, ensuring an efficient and compliant storage environment.
Challenegs faced by client
● Non-Uniform Air Distribution – Ensuring even airflow with multiple diffuser types (jet & square) and optimized locations to prevent stagnant zones.
● Heat Dissipation Management – Regulating temperature within the acceptable range despite heat sources from lighting, equipment, and external factors.
● Humidity Control – Maintaining relative humidity (RH) below 60% to prevent moisture buildup and condensation risks.
● Eliminating Hot Spots – Preventing localized overheating that could compromise pharmaceutical product stability.
● Energy Efficiency – Reducing overcooling and optimizing HVAC operation to minimize energy consumption.
● Regulatory Compliance – Meeting cGMP storage conditions by maintaining consistent temperature and airflow control.
● Complex Airflow Pathways – Addressing recirculation zones and airflow restrictions due to warehouse layout and shelving.
technology used by shirsh
● 3D Geometric Modeling – Created a detailed warehouse model incorporating racks, diffusers, and airflow pathways.
● Meshing Techniques – Applied Polyhex core mesh with prism layers for accurate boundary-layer resolution.
● Computational Fluid Dynamics (CFD) Software – Used for simulating airflow, temperature distribution, and humidity levels in the pharma warehouse area.
● Turbulence Modeling – Used Reynolds-Averaged Navier-Stokes (RANS) equations with an appropriate turbulence model for precise airflow predictions.
● HVAC System Components – Integrated multiple diffuser types (jet and square) and risers to create accurate scenarios and for airflow optimization.
● Thermal & Humidity Analysis – Simulated heat dissipation sources and moisture control to maintain stability.
● Optimization Algorithms – Applied iterative solver techniques to refi ne air distribution and energy efficiency.
engineering solutions and methodology adopted
In the heart of a state-of-the-art pharmaceutical warehouse, the challenge was clear: achieving optimal air distribution while maintaining precise environmental control. The client provided us with critical inputs, including the 2D warehouse layout, HEPA filter sizes, riser sizes, equipment details, and the locations of HEPA filters and risers. Additionally, supply temperature, humidity, and air velocity data were shared to ensure a comprehensive analysis.
Using this data, our team developed a detailed 3D model of the facility, accurately representing the HVAC system and its interaction with the environment. A high-quality computational mesh was generated, incorporating Polyhex core meshing with prism layers to resolve boundary layers accurately. Each boundary condition—temperature, velocity, humidity, and multiple heat loads from equipment, lighting, and external sources—was carefully applied to simulate real-world conditions.
The initial CFD analysis revealed critical issues: temperature and humidity levels were out of the required limits, posing risks to product stability. Stagnant zones led to uneven cooling, and improper airflow distribution resulted in localized overheating and humidity buildup. These inefficiencies could have compromised pharmaceutical storage conditions, leading to potential regulatory non-compliance.
To address these issues, we proposed strategic modifications. The HEPA and riser locations were adjusted to optimize airflow distribution, ensuring better mixing and eliminating stagnant zones. Additionally, modifications to the supply temperature and humidity levels were recommended to stabilize environmental conditions across the facility. The revised configuration improved dehumidification efficiency and prevented condensation risks by maintaining relative humidity below 60%.
With these refinements, the final simulation results demonstrated a significant improvement. Uniform cooling at 20°C was achieved, with optimized airflow velocities ranging between 0.28 – 0.78 m/s. Hotspots were eliminated, and airflow pathways were adjusted to minimize pressure drops, enhancing overall system efficiency. These changes ensured compliance with cGMP and pharmaceutical storage regulations, validating our approach against industry standards.
Through a combination of precise engineering, advanced CFD simulations, and strategic optimizations, we successfully transformed the facility’s air distribution system. The outcome was a highly efficient HVAC setup that met all regulatory requirements while optimizing energy consumption—setting a new benchmark in pharmaceutical storage environmental control.
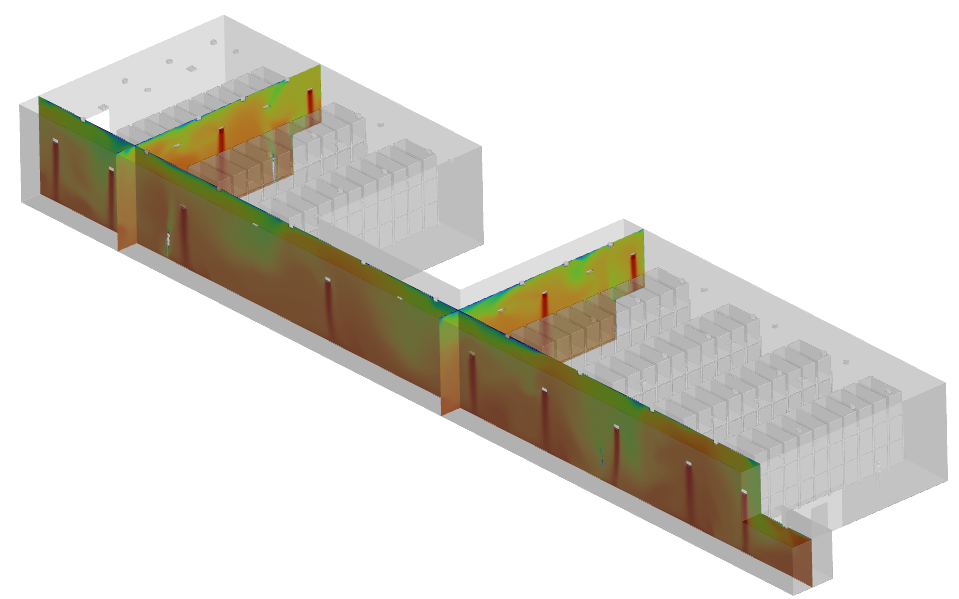
HUMIDITY GRADIENT INSIDE WAREHOUSE
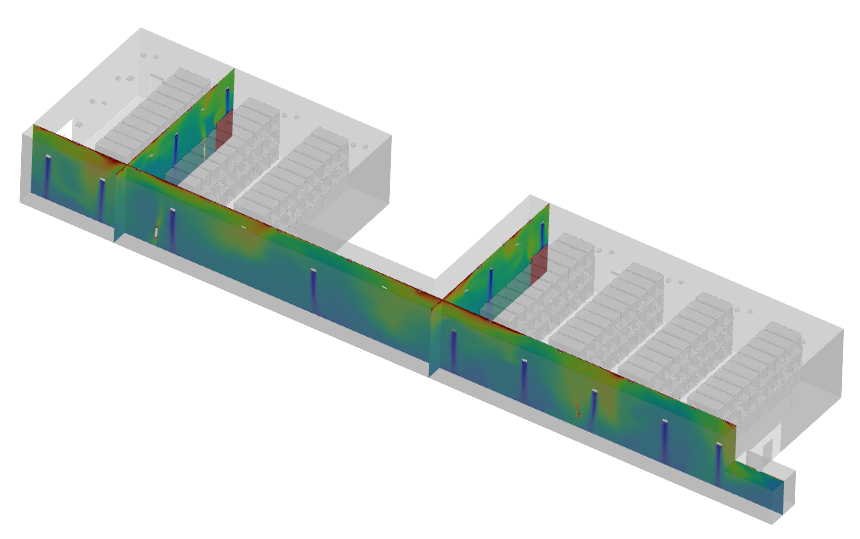
TEMPERATURE GRADIENT INSIDE WAREHOUSE
benefits to client
Precise Temperature Control
● Achieved an average temperature of 20°C, ensuring uniform cooling across the warehouse.
● Eliminated hot spots that could degrade temperature-sensitive pharmaceuticals.
Enhanced Airflow Distribution
● Eliminated stagnant zones, maintaining an optimal air velocity range of 0.28 – 0.78 m/s.
● Improved ventilation efficiency with optimized diffuser placement.
Humidity Stability & Moisture Control
● Maintained relative humidity (RH) below 60%, preventing condensation risks.
● Enhanced dehumidifi cation strategies for consistent moisture control.
Regulatory Compliance & Product Safety
● Ensured adherence to cGMP storage conditions for pharmaceutical warehousing.
● Provided a stable environment that prevents contamination and degradation of sensitive products.
Energy Efficiency & Cost Savings
● Prevented overcooling, leading to reduced HVAC energy consumption.
● Optimized airflow patterns to minimize system pressure drop, enhancing operational efficiency.
Data-Driven Decision Making
● CFD analysis provided quantifiable insights for system adjustments and performance validation.
● Allowed predictive analysis for future scalability and HVAC system enhancements.
Improved Operational Reliability
● Optimized air distribution reduced HVAC maintenance requirements.
● Enhanced system stability ensures consistent warehouse conditions without frequent recalibrations.
This CFD-driven optimization delivered a cost-effective, energy-efficient, and fully compliant HVAC system for pharmaceutical storage, ensuring product integrity and operational reliability.
About Client
Pharma Access is a leading provider of turnkey solutions for the pharmaceutical industry, specializing in the design, engineering, and execution of GMP-compliant facilities. With a strong focus on innovation, regulatory compliance, and operational efficiency, Pharma Access delivers cutting-edge solutions for cleanrooms, manufacturing plants, and storage facilities. Their expertise spans across HVAC systems, cleanroom technology, process engineering, and regulatory consulting, ensuring pharmaceutical companies achieve optimal production and storage conditions.
let's connect to work together
Have a project in mind or need expert guidance? We’re here to help! Connect with us to discuss your engineering simulation, product development, or automation needs. Fill out the form, and our experts will get in touch with you soon.