Case Study Compiled by
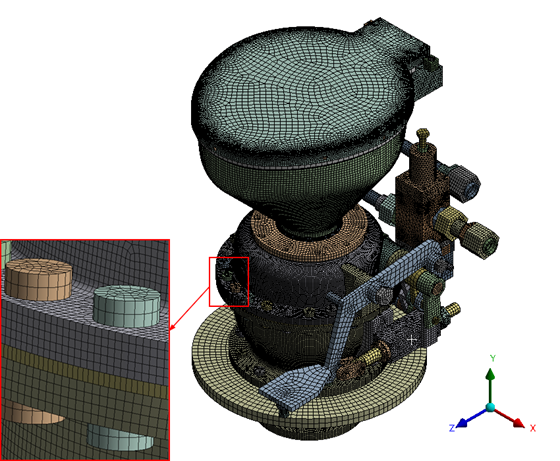
HEXAHEDRAL MESH OF WC PAN
Brief of case study
This case study explores how FEA analysis was applied to optimize the structural stability of a WC PAN unit used in defence industry based submarine applications under various operational loads, including pressure, vibration, and shock. The FEA simulation analyzed material strength, stress distribution, and deformation under critical conditions. By evaluating structural integrity, high-stress concentration areas, and fatigue life, the study highlights key improvements such as optimized material selection, enhanced load-bearing capability, and improved design reliability. The refined WC PAN design ensures compliance with JSS55555 standards, improves longevity, and minimizes failure risks under extreme operating conditions.
Challenegs faced by client
- Pressure Load Evaluation – Assessing the WC PAN’s ability to withstand operating and hydrostatic test pressures without excessive deformation or failure.
- Shock and Vibration Effects – Ensuring structural integrity under transient shock loads and dynamic vibrations in multiple directions.
- Fatigue Life Prediction – Evaluating material endurance under cyclic loading to prevent premature failures.
- Material Strength Optimization – Balancing cost, weight, and corrosion resistance while ensuring compliance with industry standards.
- Connection Integrity – Assessing the load-bearing capacity of bolted joints and seals under high pressure conditions.
- Regulatory Compliance – Verifying design adherence to JSS55555 and other safety standards for structural reliability.
- Computational Complexity – Managing high fidelity meshing, solver settings, and computational time for accurate FEA simulations.
technology used by shirsh
- 3D Geometric Modeling – Developed a detailed CAD model of the WC PAN, incorporating precise geometry, material properties, and connection details.
- Advanced Meshing Techniques – Applied Hexahedral and Tetrahedral meshing for FEA to ensure accurate resolution of stress distributions and structural deformations.
- Finite Element Analysis (FEA) Software – Utilized ANSYS 2020R1 to evaluate structural deformations, stresses, and load-bearing capacity under various operating conditions.
- Pressure & Load Simulations – Simulated operating pressure, hydrostatic test pressure, and transient shock loads to assess real-world performance.
- Vibration & Fatigue Analysis – Conducted frequency and fatigue life analysis to predict long-term durability under cyclic loading.
- Bolt Pretension & Contact Modeling – Simulated bolt loads and frictional interactions to ensure proper sealing and joint stability.
- Optimization Techniques – Iterative solver methods were used to refine structural reinforcements while maintaining a balance between weight and strength.
engineering solutions and methodology adopted
For the structural analysis of the WC PAN, the primary objective was to ensure structural stability under pressure, vibration, and shock loads, critical for its submarine application in the defence industry. The WC PAN is designed to operate under extreme conditions, including high-pressure environments and dynamic loads encountered during submarine operations.
The client provided key inputs, including 2D design layouts, material specifications, and operational loading conditions, such as pressure and mechanical stresses. Using this data, our team created a detailed 3D model of the WC PAN, incorporating all critical structural elements. A finite element (FE) model was developed to analyze stress distribution, deformation patterns, and load-bearing capacity under real-world conditions.
High-quality hexahedral meshing was applied to ensure accurate stress and displacement predictions. To achieve a realistic pressure response, the simulation incorporated operating pressure and hydrostatic test pressure conditions, simulating the extreme environments faced in submarine operations. The FEA simulation revealed localized high-stress concentrations near bolted connections and sealing areas, indicating potential failure points under submarine conditions.
To address these challenges, contact modeling and bolt pretension analysis were performed, optimizing joint stability and sealing effectiveness. The initial analysis highlighted excessive stress in critical regions, which posed a risk to structural integrity during submarine deployment. A non-linear analysis was conducted, introducing design modifications that significantly reduced stress levels and improved deformation behavior.
The final design achieved optimal structural performance, with all stress values well within acceptable limits, ensuring compliance with JSS55555 standards for defense applications. These refinements strengthened high-stress regions, improved joint stability, and enhanced long-term durability, making the WC PAN suitable for demanding submarine environments.
Through precise engineering, advanced FEA simulations, and strategic optimizations, the WC PAN now meets defence industry standards, ensuring reliable performance and extended service life in submarine applications.
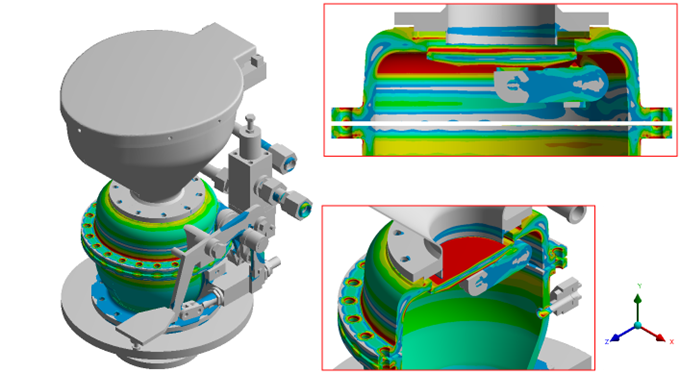
INTERNAL PRESSURE ANALYSIS RESULT PLOT
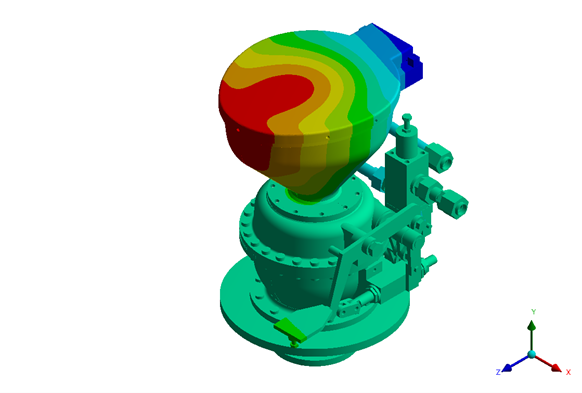
VIBRATION ANALYSIS RESULT PLOT
benefits to client
-
Enhanced Load Resistance & Structural Stability
- Withstood operating and hydrostatic test pressures with minimal deformation.
- Identified high-stress zones and reinforced critical sections to improve load distribution.
-
Optimized Connections & Joint Strength
- Advanced FEA simulations and bolt pretension modeling ensured secure load-bearing connections.
- Prevented leakage and joint failure under high-pressure conditions with optimized sealing mechanisms.
-
Regulatory Compliance & Safety
- Design modifications ensured full compliance with JS55555 standards for stress, deformation, and fatigue life.
- Improved structural integrity enhanced safety and long-term operational reliability.
-
Extended Reliability & Longevity
- Enhanced fatigue resistance and vibration durability for long-term reliability.
- Minimized maintenance needs and ensured extended service life.
Through precise engineering, advanced FEA simulations, and strategic optimizations, we delivered a stable, compliant WC PAN design, ensuring durability, safety, and long-term performance under extreme conditions.
About Client
Esteedee Autocom Engineers is a renowned manufacturer specializing in hydrodynamic bearings, heat exchangers, and precision engineered components for a wide range of industries. With over 35 years of expertise, the company has established itself as a trusted provider of high performance, durable, and reliable solutions tailored to meet diverse client needs. Their capabilities extend to OEM design, advanced stress and thermal analysis, vibration testing, and white metal bearing refurbishment, ensuring compliance with the highest industry standards. Through cutting edge engineering techniques and a customer-focused approach, Esteedee Autocom Engineers delivers cost-effective, high-quality solutions that enhance operational efficiency, longevity, and overall system performance.
let's connect to work together
Have a project in mind or need expert guidance? We’re here to help! Connect with us to discuss your engineering simulation, product development, or automation needs. Fill out the form, and our experts will get in touch with you soon.